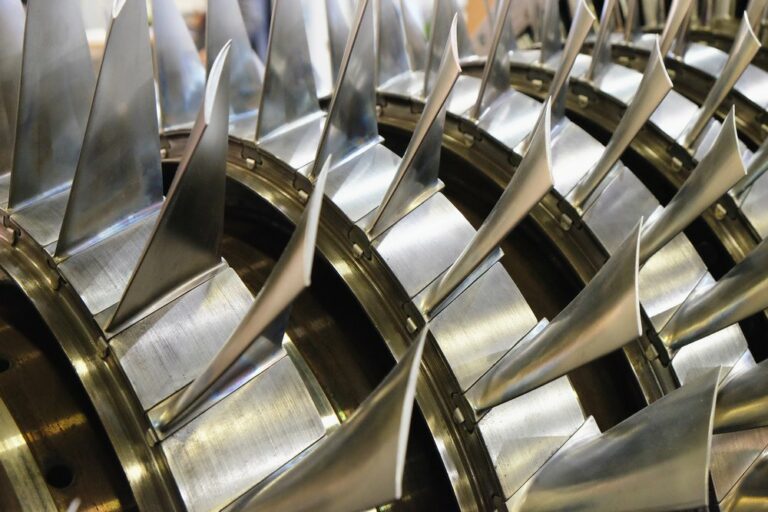
Welcome to the fascinating world of gas turbine blades, a realm where precision engineering meets cutting-edge technology. These blades are more than just components; they are the heart of modern propulsion and energy systems, playing a pivotal role in everything from jet engines to power plants. Their design and functionality epitomize human ingenuity and our relentless pursuit of efficiency and performance.
In this blog, we will delve into the various types of gas turbine blades, each showcasing a unique blend of material science, aerodynamics, and engineering prowess. Join us as we unravel the complexities and innovations that define these technological marvels.
Basics of Gas Turbine Blades
Gas turbine blades are engineered to withstand extreme conditions while efficiently converting energy. Typically made from superalloys, these blades are a testament to modern metallurgy and aerodynamic design.
Types of Gas Turbine Blades
There are several gas turbine types, each designed for specific roles and operational requirements. Let’s delve into these various types.
Compressor Blades
Compressor blades, crucial for increasing air pressure in engines, are designed for durability and efficiency. They are often made from titanium or steel alloys for optimal performance.
Turbine Blades
Turbine blades are at the heart of energy generation. They must resist high temperatures and rotational forces, which is why materials like nickel-based superalloys are commonly used.
Fan Blades
In jet engines, fan blades play a vital role. Their unique aerodynamic design aids in air intake efficiency. Composite materials are increasingly popular for these blades due to their strength-to-weight ratio.
Single Crystal Blades
Single crystal blades offer superior strength and resistance to thermal creep compared to polycrystalline counterparts. Their manufacturing process is complex but results in remarkable performance enhancements.
Directionally Solidified Blades
These blades are a step between single crystal and polycrystalline blades. They have grains aligned in one direction, offering better thermal resistance than traditional polycrystalline blades, and are particularly useful in high-heat applications.
Evolution of Blade Design
The design of gas turbine blades has evolved significantly over the years. From simple metal alloys to advanced superalloys and composite materials, this evolution reflects the technological advancements and increasing demands of modern engines.
Impact on Efficiency and Performance
The efficiency and performance of a gas turbine are heavily influenced by the blade design. Innovations in blade technology directly contribute to improved fuel efficiency and enhanced overall engine performance.
Aerodynamic Design
Aerodynamic design is crucial for maximizing the efficiency of turbine blades. Recent innovations focus on optimizing the blade shape and surface to reduce drag and increase airflow efficiency.
Cooling Techniques
To withstand high operating temperatures, advanced cooling techniques are employed in turbine blade design. These methods, such as internal air channels and thermal barrier coatings, are essential for prolonging the lifespan of the blades.
Future Trends in Blade Technology
As we gaze into the horizon of gas turbine technology, several emerging trends and innovations promise to redefine the future of blade design and functionality. These advancements are not just incremental improvements but are poised to revolutionize the way we think about turbine efficiency, durability, and environmental impact.
Advanced Materials and Coatings
The quest for materials that can withstand extreme temperatures and stresses continues to drive research and development. Future turbine blades are likely to utilize even more advanced superalloys, ceramics, and metal matrix composites. These materials offer higher temperature tolerances and greater strength-to-weight ratios. Additionally, breakthroughs in thermal barrier coatings are expected to further enhance the thermal efficiency and longevity of blades by providing better protection against heat and oxidation.
Innovative Manufacturing Techniques
Additive manufacturing, commonly known as 3D printing, is set to play a significant role in the production of turbine blades. This technology allows for more complex geometries and internal structures, which are impossible to achieve with traditional manufacturing methods. It also enables quicker prototyping and customization, reducing the time and cost of blade development.
Wrapping Up
With this, it’s clear that these components are not just mere pieces of metal but are, in fact, critical catalysts in the evolution of energy and propulsion technologies. They exemplify how continuous innovation can lead to remarkable advancements in efficiency, performance, and sustainability.
Looking ahead, the future of gas turbine blade technology shines bright with potential, driven by emerging materials and groundbreaking design techniques. These blades do more than power our machines; they power our progress and our relentless quest to push the boundaries of what’s possible. In the world of gas turbine blades, we see not just the reflection of our current technological achievements but also the promise of a more efficient, powerful, and sustainable tomorrow.
Also, discover your ideal power solution with Life Cycle Power, where we design, engineer, and maintain the most optimal turnkey power solutions in jersey village, Texas tailored to your electrical needs.